Global Membrane Contactor Market, By Function (Hydrophobic, Hydrophilic), Membrane Type (Polypropylene, Polytetrafluoroethylene), End-use (Food Processing, Water & Wastewater Treatment, Pharmaceutical Processing, Power & Steam Generation, Oil & Gas, Microelectronics & Semiconductors), and Region – Industry Analysis and Forecast to 2030
The global membrane contactor market is expected to grow from USD 288.5 million in 2023 to USD 447.6 million by 2030 at a CAGR of 6.5%. The market is driven by factors such as the increasing industrial demand for efficient separation processes, water and wastewater treatment, growing interest in carbon capture and sequestration (CCS), pharmaceutical and biotechnology industry growth, food and beverage industry advancements, emerging applications in oil and gas, innovations in membrane technology, stringent environmental regulations, and global water scarcity challenges. These drivers collectively contribute to the expansion of the membrane contactor market, making it a critical component in various industrial processes aimed at improving efficiency, sustainability, and environmental compliance.
Figure 1: Global Membrane Contactor Market Size, 2023-2030 (USD Million)
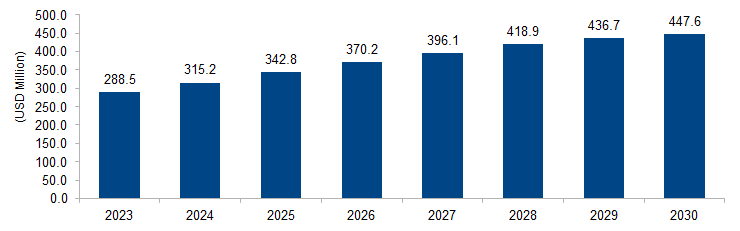
Source: Secondary Research, Expert Interviews, and MAARECO Analysis
A membrane contactor is a specialized device used for efficient gas-liquid or liquid-liquid contact and separation processes. It consists of a porous membrane that acts as a physical barrier between two phases while allowing selective transport of specific components. The membrane’s structure enables the transfer of gases or dissolved substances from one phase to another, typically enhancing mass transfer and separation efficiency.
Membrane contactors find application in diverse industries such as water treatment, pharmaceuticals, food and beverage, petrochemicals, and renewable energy. They offer advantages like reduced energy consumption, enhanced purity, and selective removal of contaminants. These devices play a pivotal role in various processes including degassing, oxygen removal, carbon capture, and extraction, contributing to improved efficiency and sustainability in industrial applications.
Membrane Contactor Market Drivers
Increasing Industrial Demand for Efficient Separation Processes
The increasing industrial demand for efficient separation processes is a significant driver propelling the growth of the membrane contactor market. Industries across the spectrum, including petrochemicals, chemicals, pharmaceuticals, and food and beverage, are continually seeking more effective methods for separation, purification, and gas-liquid contact. Membrane contactors have emerged as a highly promising solution to meet this demand.
One of the primary reasons behind this driver is the pressing need for enhanced efficiency and sustainability in industrial processes. Traditional separation methods often consume significant energy and may involve the use of chemicals, making them less environmentally friendly and economically viable. In contrast, membrane contactors offer several advantages that align with the industry’s goals for efficiency and sustainability.
Membrane contactors enable precise control over gas-liquid interactions and separations. They leverage specialized porous membranes that selectively permit the passage of specific components, such as gases or dissolved substances, while blocking others. This selective permeation enhances mass transfer efficiency, resulting in higher separation and purification rates. Moreover, these devices operate at lower temperatures and pressures compared to some traditional methods, reducing energy consumption and operational costs.
As industries increasingly prioritize sustainability, the adoption of membrane contactors is expected to continue growing. These devices offer a pathway to more resource-efficient and environmentally friendly processes, making them a key driver in addressing the evolving needs of industrial separation and purification applications. This driver boost the growth of membrane contactor market.
Water and Wastewater Treatment
The driver of water and wastewater treatment applications in the membrane contactor market is fueled by the urgent global need for effective and sustainable solutions to address water scarcity, deteriorating water quality, and wastewater management challenges. Membrane contactors have emerged as a pivotal technology in this context, offering innovative and efficient methods for water treatment and purification.
One of the primary reasons driving the adoption of membrane contactors in water treatment is their ability to efficiently remove dissolved gases and volatile organic compounds from water. These contaminants, such as oxygen, carbon dioxide, and volatile organic compounds, can affect water quality, impact industrial processes, and pose environmental concerns. Membrane contactors excel in degassing and deaeration applications by utilizing selective membranes to remove these substances, leading to improved water quality and enhanced operational efficiency.
Moreover, membrane contactors play a crucial role in processes like desalination and brackish water treatment, where the removal of dissolved ions and contaminants is essential to make water suitable for consumption and industrial use. Their precision and effectiveness in separating salt and other impurities from saline water sources contribute to the production of freshwater, addressing water scarcity challenges in arid regions.
In wastewater treatment, membrane contactors aid in the removal of volatile organic compounds and other contaminants from industrial effluents, ensuring compliance with environmental regulations and the protection of aquatic ecosystems. Their efficiency in reducing chemical oxygen demand (COD) and biological oxygen demand (BOD) in wastewater streams makes them an indispensable tool in sustainable wastewater management. These factors strengthen the growth of membrane contactor market.
Membrane Contactor Market Restraints
High Initial Costs
High Initial Costs represent a significant restraint in the membrane contactor market. The deployment of membrane contactor systems often involves substantial upfront expenses, which can act as a deterrent for potential users, particularly in industries or regions with limited capital budgets. There are several factors contributing to these initial costs.
Firstly, the procurement of membrane contactor equipment itself can be relatively expensive. High-quality membranes, specialized materials, and precision engineering are essential components of membrane contactor systems, all of which contribute to their initial price tag.
Secondly, installation and integration expenses can add significantly to the total cost. Membrane contactors need to be carefully integrated into existing industrial processes or water treatment systems. This integration requires engineering expertise, potentially necessitating modifications to existing infrastructure or the development of custom solutions, all of which entail additional costs.
Thirdly, there are considerations related to infrastructure and utilities. In some cases, users may need to invest in ancillary equipment, such as pumps, storage tanks, and monitoring systems, to ensure the membrane contactor system operates effectively. Moreover, membrane contactors may require specialized utility connections like specific water or gas feeds, which can involve additional setup and operational costs.
Finally, there are ongoing operational and maintenance expenses. While initial costs are a significant concern, users must also account for expenses associated with membrane replacement, routine maintenance, and system monitoring to ensure optimal performance over time, acting as restraining factors for the membrane contactor market.
Membrane Fouling
Membrane fouling represents a significant restraint in the membrane contactor market. Fouling occurs when undesirable substances, such as particles, microorganisms, or contaminants, accumulate on or within the membrane’s surface or pores, impeding the efficient flow of liquids or gases through the membrane. This accumulation diminishes the effectiveness and efficiency of the membrane contactor system, creating several challenges.
Firstly, fouling leads to a decrease in overall system performance. It hampers mass transfer rates, reduces separation efficiency, and impedes the flow rate, ultimately impacting productivity. This compromises the benefits associated with using membrane contactors, such as energy efficiency and enhanced separation.
Secondly, fouling necessitates frequent maintenance and cleaning. Cleaning procedures can be time-consuming, costly, and may involve harsh chemicals or specialized cleaning equipment. These cleaning efforts result in system downtime and operational disruptions.
Furthermore, fouling can affect the lifespan of the membranes themselves. Frequent fouling and cleaning can lead to membrane degradation, reducing their longevity and necessitating more frequent replacements. This contributes to higher operational costs over the membrane contactor’s lifespan.
To mitigate fouling, ongoing research and development efforts focus on designing fouling-resistant membranes and developing innovative fouling mitigation strategies. Addressing fouling challenges is crucial for maximizing the efficiency and cost-effectiveness of membrane contactors in various industries, including water treatment, gas-liquid contact processes, and more. These factors restrain the growth of membrane contactor market.
Membrane Contactor Market Opportunities
Carbon Capture and Sequestration (CCS)
The opportunity presented by Carbon Capture and Sequestration (CCS) is a pivotal driver in the membrane contactor market. CCS is becoming increasingly critical in the global effort to combat climate change by capturing carbon dioxide (CO2) emissions from industrial processes and power plants before they are released into the atmosphere and sequestering or storing them safely. Membrane contactors are emerging as a key technology in CCS applications.
In CCS processes, membrane contactors play a crucial role in selectively capturing CO2 from industrial flue gases. These specialized devices utilize porous membranes to facilitate the efficient separation of CO2, allowing for its capture and subsequent storage or utilization. Membrane contactors offer advantages like high selectivity, compact design, and energy efficiency compared to traditional absorption-based methods.
The global focus on reducing greenhouse gas emissions and meeting climate targets is driving investments in CCS technology. Governments, industries, and organizations worldwide are recognizing the urgent need for carbon capture, and membrane contactors are poised to play a vital role in enabling more efficient and cost-effective CCS systems. As CCS initiatives continue to expand, the demand for advanced membrane contactor solutions is expected to grow significantly, presenting a substantial opportunity for membrane contactor manufacturers to contribute to global sustainability efforts while also realizing business growth. These factors provide new growth opportunities to the membrane contactor market.
Technological Advancements
The membrane contactor market presents a compelling opportunity driven by technological advancements. Ongoing research and development efforts are continually enhancing membrane materials, designs, and overall system efficiency, opening new horizons for this innovative technology.
One significant advancement is the development of novel membrane materials with improved selectivity, durability, and resistance to fouling. These materials enable membrane contactors to perform more effectively in a wide range of applications, from water treatment to gas-liquid separations.
Furthermore, advancements in membrane module design are increasing the scalability and adaptability of membrane contactors. Modular systems can be customized to fit specific industrial processes and easily integrated into existing infrastructure, making them more accessible to a broader range of industries.
The use of computational modeling and simulation techniques is also revolutionizing the membrane contactor market. These tools enable more precise system design, optimization, and prediction of performance under varying conditions, reducing the time and costs associated with trial-and-error experimentation.
Moreover, technological advancements are driving the development of smarter, more automated membrane contactor systems. Automation and real-time monitoring improve operational efficiency, reduce maintenance costs, and enhance the reliability of these systems, making them more attractive to industries with stringent quality and safety requirements.
As technology continues to evolve, membrane contactors are becoming more energy-efficient, cost-effective, and environmentally friendly, positioning them as key players in addressing critical challenges such as clean water access, greenhouse gas emissions reduction, and sustainable industrial processes. The ongoing pursuit of technological excellence in membrane contactor development ensures a promising future for this market across diverse applications and industries.
Thus, these technological advancements offer new opportunities to the membrane contactor market.
Membrane Contactor Market Challenges
Limited Application Scope
The limited application scope is a notable challenge in the membrane contactor market. Membrane contactors are highly specialized devices, each tailored to specific separation or purification processes. While they excel in these niche applications, this specialization can limit their versatility and adaptability to a broader range of industrial processes.
One reason for this challenge is that membrane contactors are typically designed with specific membrane materials and configurations optimized for particular tasks. For example, a membrane contactor used for oxygen removal in water treatment may have a different membrane structure and material compared to one used for carbon dioxide capture in gas streams. Consequently, adapting a membrane contactor to a different application often requires redesigning the system, selecting appropriate membranes, and fine-tuning the operating parameters.
Moreover, the diverse nature of industrial processes and separation requirements means that no single membrane contactor can serve all needs. This specialization can make it challenging for membrane contactor manufacturers to offer standardized, off-the-shelf solutions applicable across various industries.
As a result, potential users must carefully assess whether a membrane contactor aligns with their specific needs and whether the benefits of its high selectivity, efficiency, and environmental sustainability outweigh the limitations of its specialized design. This challenge underscores the importance of ongoing research and development efforts to expand the application scope of membrane contactors, making them more adaptable and accessible to a wider array of industries and processes.
Membrane Material Durability
Membrane material durability is a notable challenge in the membrane contactor market. Membrane contactors rely on specialized membranes to facilitate gas-liquid or liquid-liquid separations. These membranes must endure harsh operating conditions, including exposure to aggressive chemicals, high temperatures, and varying pressures, while maintaining their structural integrity and separation efficiency.
One key challenge is ensuring that the selected membrane materials can withstand the specific conditions of a given application. For instance, in industrial processes involving corrosive chemicals or extreme pH levels, membranes must resist chemical degradation and maintain their performance over time. Failure to do so can lead to a shorter membrane lifespan, increased maintenance costs, and operational disruptions.
Additionally, membrane materials must endure thermal stresses, especially in applications where high temperatures are involved. Thermal cycling can cause material expansion and contraction, potentially leading to membrane damage or delamination.
Furthermore, membrane durability is essential for applications in which membranes are exposed to abrasive particles or biological fouling, such as in wastewater treatment. Prolonged exposure to these contaminants can degrade membrane materials, reducing their efficiency and necessitating more frequent replacements.
To address this challenge, ongoing research and development efforts focus on the development of more robust and durable membrane materials, including advanced polymers and coatings. Additionally, manufacturers must provide proper guidance on membrane selection and maintenance practices to ensure the longevity and performance of membrane contactor systems, particularly in demanding industrial environments.
Regional Trends
North America:
Growing Industrial Applications: North America has seen increased adoption of membrane contactors in industries like pharmaceuticals, food and beverage, and petrochemicals for various separation and purification processes.
Stringent Environmental Regulations: Strict environmental regulations have driven the demand for advanced water and wastewater treatment solutions, including membrane contactors.
Research and Development: The region is known for its active research and development efforts, leading to innovations in membrane materials and technology.
Europe:
Water Scarcity Solutions: European countries have been investing in advanced water treatment technologies to address water scarcity issues. Membrane contactors are increasingly used in desalination and drinking water production.
Focus on Sustainability: The European Union’s emphasis on sustainability and reducing carbon emissions has led to the adoption of membrane contactors in carbon capture and sequestration (CCS) projects.
Biotechnology: The pharmaceutical and biotechnology sectors in Europe have been utilizing membrane contactors for applications in bioprocessing and gas-liquid separations.
Asia Pacific:
Industrial Growth: The rapid industrialization in Asia Pacific countries, especially China and India, has led to a surge in demand for membrane contactors in various industrial applications, such as chemicals and petrochemicals.
Water Treatment: Asia Pacific faces water scarcity challenges in many regions, driving the adoption of advanced water treatment technologies, including membrane contactors.
Renewable Energy: Asia Pacific has been investing in renewable energy projects, including hydrogen production, which uses membrane contactors for gas separation.
Middle East and Africa:
Desalination: Middle East and Africa countries are prominent users of membrane contactors in desalination plants to produce freshwater from seawater, addressing their water scarcity issues.
Oil and Gas: The oil and gas industry in this region uses membrane contactors for various applications, including natural gas sweetening.
South America:
Mining Industry: South America’s mining industry has shown an interest in using membrane contactors for applications such as metal recovery and wastewater treatment.
Environmental Concerns: Environmental regulations and concerns have led to an increased focus on water and wastewater treatment solutions, creating opportunities for membrane contactors.
Key Players
Key players operating in the global membrane contactor market are 3M, Romfil, Hangzhou Cobetter Filtration Equipment Co., Ltd., Compact Membrane Systems, Wuhan Tanal Industrial Co., Ltd., JU.CLA.S Srl, Veolia Water Technologies, Inc., PTI Pacific Ptyltd., Eurowater, KH TEC GmbH, and Hydro-Elektrik GmbH.
PRICE
ASK FOR FREE SAMPLE REPORT