Global Lithium-ion Battery Binders Market, By Type (Anode Binders, Cathode Binders), Battery Chemistry (Lithium Iron Phosphate, Lithium Nickel Manganese Cobalt, Lithium Cobalt Oxide, Lithium Titanate Oxide), Material (Polyvinylidene Fluoride, Polymethyl Methacrylate, Carboxymethyl Cellulose, Styrene Butadiene Copolymer), Industry Application (Consumer Electronics, Automotive, Energy Storage, Industrial), and Region – Industry Analysis and Forecast to 2030
The global lithium-ion battery binders market is expected to grow from USD 1.81 billion in 2023 to USD 4.66 billion by 2030 at a CAGR of 14.5%. The market is driven by factors such as the growing demand for electric vehicles (EVs) and portable electronics, advancements in battery technology, efforts to enhance battery performance, rising renewable energy integration, consumer electronics and wearables market, global sustainability initiatives, and investments in battery manufacturing infrastructure. The drivers for the lithium-ion battery binders market are closely linked to the broader trends of electrification, renewable energy adoption, and technological innovation. As these trends continue to evolve, the demand for high-quality binders that contribute to improved battery performance and durability is expected to remain strong.
Figure 1: Global Lithium-ion Battery Binders Market Size, 2023-2030 (USD Billion)
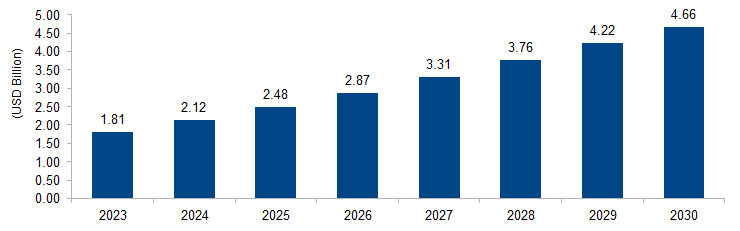
Source: Secondary Research, Expert Interviews, and MAARECO Analysis
Lithium-ion battery binders are essential components used in the fabrication of lithium-ion batteries, which power a wide range of devices such as electric vehicles, portable electronics, and energy storage systems. These binders are specialized materials that serve as adhesives, holding together the active materials within battery electrodes, such as cathodes and anodes, and ensuring their structural integrity.
By securely bonding electrode materials to the current collectors and maintaining their proper arrangement, binders enhance the overall stability, performance, and cycle life of lithium-ion batteries. They play a vital role in minimizing the loss of active material during charge and discharge cycles, reducing electrode degradation, and improving the electrical conductivity within the battery cell.
Lithium-ion battery binders contribute to the efficient operation and longevity of batteries, which are integral components in the transition towards cleaner energy and the electrification of various industries.
Lithium-ion Battery Binders Market Drivers
Growing Demand for Electric Vehicles (EVs) and Portable Electronics
The escalating demand for electric vehicles (EVs) and portable electronics serves as a significant driver propelling the lithium-ion battery binders market. The global push towards cleaner and more sustainable transportation, exemplified by the rise of electric vehicles, is reshaping the automotive industry. EVs rely heavily on lithium-ion batteries due to their energy density, lightweight nature, and rechargeable capabilities. Binders, as crucial components within these batteries, play an integral role in maintaining the structural integrity of electrodes. They ensure that active materials, like cathodes and anodes, remain securely affixed to the electrodes and current collectors, contributing to the battery’s overall stability and longevity.
Furthermore, the surge in demand for portable electronics, encompassing smartphones, laptops, wearables, and other devices, further drives the necessity for efficient and high-performing lithium-ion batteries. Binders enable the creation of electrodes that can withstand repeated charging and discharging cycles, a critical requirement for these devices. As consumers increasingly rely on these gadgets for work, communication, and entertainment, the pressure to enhance battery life and performance intensifies. Binders, by enhancing adhesion and maintaining electrode integrity, contribute to the extended lifespan, faster charging, and higher energy density that consumers seek.
In essence, the growth in EVs and portable electronics amplifies the demand for lithium-ion batteries, consequently influencing the requirement for advanced binders. Manufacturers are pushed to develop binders that can accommodate the unique requirements of these industries, including improved energy density, higher efficiency, and enhanced cycle life. As the adoption of electric vehicles and the ubiquity of portable electronics continue to expand, the need for superior battery components like binders remains a driving force within the lithium-ion battery binders market.
Efforts to Enhance Battery Performance
The driver of efforts to enhance battery performance plays a pivotal role in propelling the lithium-ion battery binders market forward. As the demand for more efficient, longer-lasting, and high-performing batteries grows across industries, battery manufacturers are actively seeking ways to optimize the capabilities of lithium-ion batteries. Binders, as essential components within battery electrode manufacturing, contribute significantly to achieving these performance improvements.
Battery manufacturers are focusing on increasing energy density, cycle life, and charging rates of lithium-ion batteries to meet the evolving needs of applications such as electric vehicles, portable electronics, and renewable energy storage. Binders are crucial in achieving these goals by ensuring the structural integrity of electrodes and maintaining consistent electrode composition during repeated charge and discharge cycles. They help prevent the detachment of active materials from the electrode, which can lead to capacity fading and reduced battery performance over time.
Furthermore, as battery technology advances, the use of novel electrode materials and designs becomes more prevalent. Binders play a critical role in accommodating these changes by providing the adhesive strength required to hold together diverse materials and complex structures. They aid in forming uniform electrode coatings and interfaces, reducing internal resistance and improving overall battery efficiency.
In conclusion, the drive to enhance battery performance acts as a catalyst for innovation and growth within the lithium-ion battery binders market. The collaborative efforts of battery manufacturers and binder suppliers are crucial in developing advanced binder formulations that support the ever-evolving demands of battery technology, ultimately leading to more efficient, reliable, and high-performance energy storage solutions.
Lithium-ion Battery Binders Market Restraints
Technical Challenges and Compatibility
The restraint of technical challenges and compatibility significantly influences the lithium-ion battery binders market. Developing binders that exhibit optimal performance across a diverse range of electrode materials, electrolytes, and manufacturing processes is a complex endeavor. Lithium-ion batteries employ various electrode chemistries, such as nickel-cobalt-manganese (NCM), lithium iron phosphate (LFP), and nickel-cobalt-aluminum (NCA), each with distinct material properties. Creating binders that can effectively adhere to and stabilize these diverse materials, while maintaining their electrochemical properties, poses intricate technical challenges.
Moreover, ensuring compatibility with different electrolyte formulations and separators is essential to prevent degradation or undesirable reactions within the battery cell. Binders must not only possess strong adhesion but also be chemically inert to the surrounding components, avoiding adverse interactions that could compromise battery performance or safety.
The complexity is further heightened by the need to accommodate various manufacturing processes, including electrode coating methods, solvent choices, and electrode thicknesses. Achieving uniform binder distribution and adhesion in these diverse conditions requires precise formulation and meticulous process control.
As the lithium-ion battery market continues to evolve with innovations in battery chemistry and design, binder manufacturers must remain adaptable to these changes. Developing binders that are versatile enough to accommodate new materials and evolving battery architectures is critical.
Addressing the restraint of technical challenges and compatibility requires extensive research and development efforts. Collaborations between binder manufacturers, battery researchers, and manufacturers are essential to overcome these hurdles. Through careful formulation design, testing, and optimization, binders can be developed that offer the necessary versatility and performance to support the advancements and diversification within the lithium-ion battery industry.
Safety and Environmental Concerns
The restraint of safety and environmental concerns exerts a notable impact on the lithium-ion battery binders market. Safety is of paramount importance in battery technology due to the potential risks associated with thermal runaway, leakage, and other hazardous events. Binders used in lithium-ion batteries must possess excellent thermal stability and compatibility with other components to prevent the occurrence of such risks. Ensuring that binders do not contribute to battery instability, overheating, or short-circuiting is a crucial challenge. Regulatory bodies and industry standards mandate stringent safety requirements for battery materials, including binders, adding complexity to their formulation and approval processes.
Additionally, the increasing focus on environmental sustainability drives the need for binder materials that are not only safe during battery operation but also eco-friendly throughout their lifecycle. Aspects such as binder production, disposal, and end-of-life considerations come under scrutiny. Manufacturers are under pressure to develop binders that minimize environmental impact, reduce resource consumption, and adhere to principles of circular economy and green chemistry.
The restraint of safety and environmental concerns requires thorough research and testing to ensure that binder materials contribute to the overall safety and environmental objectives of the battery industry. Developing binder formulations that strike a balance between exceptional performance, safety, and environmental responsibility involves addressing challenges in material selection, production processes, and end-of-life considerations. As the push for safer and more sustainable battery technologies intensifies, manufacturers and researchers must collaborate to create binders that align with these crucial objectives while maintaining the high performance standards demanded by the lithium-ion battery market.
Lithium-ion Battery Binders Market Opportunities
Renewable Energy Storage
The opportunity in renewable energy storage holds significant promise for the lithium-ion battery binders market. With the global shift towards cleaner and more sustainable energy sources, the integration of renewable energy, such as solar and wind, into the power grid is accelerating. However, renewable energy generation is intermittent, and energy storage systems (ESS) are essential for storing excess energy during periods of high production and supplying it during times of low production or high demand.
Lithium-ion batteries have emerged as a preferred choice for ESS due to their high energy density, rapid charging capabilities, and long cycle life. Binders play a crucial role in optimizing the performance and stability of battery electrodes within these systems. By ensuring strong adhesion between electrode materials and current collectors, binders contribute to maintaining consistent battery performance over multiple charge-discharge cycles, a vital factor in the reliability of ESS.
As the demand for renewable energy storage solutions increases, binder manufacturers have the opportunity to develop specialized formulations that cater to the specific needs of energy storage applications. Binders that enhance the thermal stability of battery electrodes, improve cycle life, and withstand the demands of grid-scale energy storage systems are in high demand. By addressing these requirements, binder manufacturers can support the growth of renewable energy integration, help stabilize power grids, and enable the efficient use of clean energy resources.
Furthermore, the opportunity extends to innovative binder materials that align with sustainability goals. Developing environmentally friendly binder solutions that reduce the overall environmental impact of ESS contributes to the industry’s commitment to sustainability. As governments and organizations worldwide invest in renewable energy infrastructure, the lithium-ion battery binders market can position itself at the forefront of enabling a greener energy future through improved battery performance and stability in renewable energy storage applications.
Research and Development Collaborations
The opportunity of research and development (R&D) collaborations holds immense potential within the lithium-ion battery binders market. As the demand for higher-performing and more efficient batteries intensifies across various industries, the complexities of binder formulations and their interactions with evolving battery technologies become increasingly intricate. R&D collaborations bring together binder manufacturers, battery researchers, academic institutions, and industry experts, fostering a collaborative environment that fuels innovation and accelerates progress.
These collaborations enable the sharing of insights, expertise, and resources, leading to the discovery of novel binder materials, formulation techniques, and application-specific solutions. By pooling their collective knowledge, participants can tackle complex challenges related to binder stability, adhesion, compatibility with diverse electrode chemistries, and safety considerations. Collaborative efforts can yield breakthroughs that enhance battery performance, extend cycle life, improve charging capabilities, and optimize overall energy storage efficiency.
Furthermore, R&D collaborations facilitate the exploration of advanced manufacturing methods, such as electrode coating processes and binder distribution techniques. Partnerships between binder manufacturers and battery researchers can result in the development of manufacturing processes that yield consistent and uniform binder application, critical for maintaining battery integrity and performance.
By fostering an environment of collaboration, research institutions and industry players can leverage each other’s strengths to overcome technical barriers and expedite the development of next-generation binder solutions. These collaborations also encourage cross-disciplinary learning, pushing the boundaries of binder technology through fresh perspectives and innovative ideas. As the energy landscape evolves, the opportunity for R&D collaborations empowers the lithium-ion battery binders market to stay at the forefront of technological advancements and contribute to the growth of sustainable energy storage solutions across industries.
Lithium-ion Battery Binders Market Challenges
Adhesion and Stability
The challenge of adhesion and stability in the lithium-ion battery binders market is a critical aspect that significantly impacts battery performance and reliability. Binders play a crucial role in maintaining the structural integrity of battery electrodes by adhering active materials to the electrode’s current collector. Ensuring strong and consistent adhesion is essential for preventing electrode degradation, electrode material detachment, and internal short circuits that can compromise battery safety and efficiency.
The intricate architecture of lithium-ion batteries, with multiple layers of electrode materials and current collectors, demands binders that can withstand the mechanical stresses encountered during charge-discharge cycles and thermal variations. Achieving enduring adhesion across numerous cycles, especially as battery designs evolve to accommodate higher energy densities and faster charging rates, poses a considerable technical challenge.
Furthermore, the stability of binders under varying operating conditions is paramount. Batteries experience temperature fluctuations, mechanical vibrations, and exposure to electrolytes, all of which can impact binder performance. Binders must remain chemically inert, not degrade, and maintain their adhesive properties under these harsh conditions to ensure consistent battery performance over the battery’s lifespan.
The challenge of adhesion and stability requires binder manufacturers to innovate and develop formulations that strike a delicate balance between strong adhesion and flexibility. They need to address these challenges while considering the compatibility of binders with different electrode materials, manufacturing processes, and battery designs. Collaborative efforts between researchers, manufacturers, and end-users are essential to overcome this challenge and ensure that binders can effectively maintain electrode integrity, ultimately contributing to the longevity, safety, and overall efficiency of lithium-ion batteries in various applications.
Compatibility with Manufacturing Processes
The challenge of compatibility with manufacturing processes is a significant hurdle in the lithium-ion battery binders market. The production of lithium-ion batteries involves intricate and varied manufacturing methods, including electrode coating, solvent choices, drying conditions, and electrode thicknesses. Binders must seamlessly integrate into these processes to ensure uniform distribution, strong adhesion, and electrode stability.
Different manufacturing techniques demand binders with varying viscosities, drying rates, and adhesion properties. Achieving consistent binder dispersion and adhesion across different electrode materials and architectures is complex. Binder manufacturers must formulate products that exhibit the right balance of flexibility and rigidity to accommodate the mechanical stresses encountered during manufacturing without compromising battery performance.
Moreover, the compatibility challenge extends to the drying and curing stages of electrode production. Binders must solidify properly without creating defects like cracks or pinholes that could undermine the battery’s structural integrity or electrochemical performance.
Addressing this challenge requires thorough understanding of the intricacies of each manufacturing process, close collaboration between binder suppliers and battery manufacturers, and rigorous testing to ensure binder performance under diverse conditions. Binder manufacturers must innovate to develop versatile formulations that can adapt to various manufacturing methods without compromising adhesion, electrode integrity, or battery safety. As manufacturing processes continue to evolve to accommodate advancements in battery technology, binder compatibility remains a dynamic challenge that influences the efficiency and reliability of lithium-ion battery production across diverse applications.
Regional Trends
Asia-Pacific: The Asia-Pacific region, particularly China, Japan, and South Korea, is a major hub for lithium-ion battery production and innovation. The rapid growth of the electric vehicle market in China drives demand for high-performance batteries and binders. These countries are at the forefront of battery technology research, encouraging advancements in binder formulations and manufacturing processes. Government initiatives to promote EV adoption further stimulate binder demand.
North America: North America, including the United States and Canada, witnesses a rising emphasis on renewable energy integration and electric mobility. As the EV market gains momentum, there’s an increasing need for advanced lithium-ion batteries and binders. Research and collaborations within the region focus on developing sustainable and efficient binder solutions that align with clean energy goals.
Europe: Europe is experiencing significant growth in the electric vehicle sector, driven by stringent emission regulations and sustainability targets. Countries like Germany, France, and the Netherlands are investing in EV infrastructure and battery manufacturing. The region’s push towards cleaner energy sources and energy storage solutions also contributes to the demand for high-quality binders for lithium-ion batteries.
Key Players
Key players operating in the global lithium-ion battery binders market are Arkema, LG Chem, Solvay, Eneos Corporation, Ashland Global Holdings Inc., BASF SE, Zeon Corporation, Crystal Clear Electronic Material Co., Ltd., Dupont, Kureha Corporation, Daikin Industries, Ltd., Fujian Blue Ocean & Black Stone Technology Co., Ltd., Sumitomo Seika Chemicals Company, Limited, Synthomer PLC, Trinseo, and Resonac Holdings Corporation.
PRICE
ASK FOR FREE SAMPLE REPORT