Global Flow Chemistry Market, By Reactor (Tubular Reactors, Oscillatory Flow Reactors, Microreactors, Photochemical Reactors, Packed-Bed Reactors, Droplet-Based Reactors), Purification Method (Chromatography, Distillation, Crystallization, Membrane Filtration, Liquid-Liquid Extraction), Application (Chemical Synthesis, Pharmaceutical Synthesis, Agrochemical Synthesis, Materials Science, Energy Conversion), and Region – Industry Analysis and Forecast to 2030
The global flow chemistry market is expected to grow from USD 1.61 billion in 2023 to USD 3.32 billion by 2030 at a CAGR of 10.9%. The market is driven by factors such as increased efficiency and safety, continuous manufacturing, reduced environmental impact, customization and innovation, pharmaceutical and fine chemical industries, academic research and collaboration, regulatory compliance and quality control, growing interest in green chemistry, advancements in automation and technology, and economic considerations. The flow chemistry market’s growth is shaped by these drivers, offering benefits to various industries, particularly in pharmaceuticals, chemicals, and academia. As technology continues to evolve and more applications are explored, the flow chemistry market is likely to expand further.
Figure 1: Global Flow Chemistry Market Size, 2023-2030 (USD Billion)
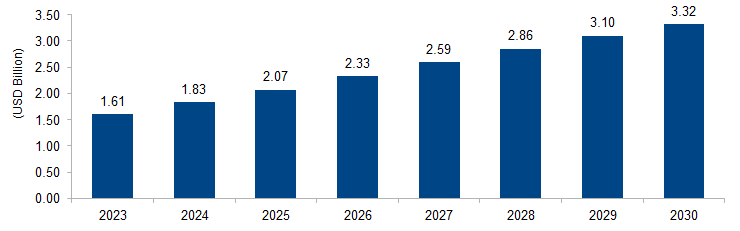
Source: Secondary Research, Expert Interviews, and MAARECO Analysis
Flow chemistry, also known as continuous flow chemistry, is a chemical synthesis approach that involves the controlled and continuous passage of reactants through a reaction system, often in microreactors or tubular reactors. In this method, instead of traditional batch processing where reactants are mixed in a single vessel, reactants are continuously pumped through a reaction system, allowing for precise control over reaction conditions such as temperature, pressure, and residence time.
Flow chemistry offers several advantages, including improved reaction efficiency, enhanced safety, reduced waste production, and the ability to synthesize complex molecules more efficiently. This approach is particularly valuable in industries like pharmaceuticals and fine chemicals, where precise control, scalability, and reproducibility of reactions are essential.
Flow chemistry enables the rapid exploration of diverse reaction conditions, optimization of processes, and the development of novel chemical pathways, making it a powerful tool for researchers and manufacturers seeking innovative and sustainable solutions for chemical synthesis.
Flow Chemistry Market Drivers
Increased Efficiency and Safety
The driver of increased efficiency and safety is a compelling force propelling the growth of the flow chemistry market. Flow chemistry revolutionizes traditional chemical synthesis processes by offering a precise and continuous approach to reactions, resulting in improved efficiency and enhanced safety measures. In contrast to batch processing, where reactants are combined in a single vessel, flow chemistry involves the controlled flow of reactants through microreactors or tubular reactors. This setup allows for meticulous control over reaction parameters such as temperature, pressure, and mixing, which in turn leads to higher yields, reduced reaction times, and enhanced selectivity.
The continuous nature of flow chemistry eliminates the need for time-consuming batch procedures, streamlining production and reducing downtime. This enhanced efficiency is particularly valuable in industries where speed to market and cost-effectiveness are crucial, such as pharmaceuticals and fine chemicals. Moreover, the controlled flow environment minimizes the risk of unwanted side reactions, making it safer for handling hazardous or sensitive reagents. The smaller scale of reactions within microreactors also means that potentially dangerous exothermic reactions can be managed more effectively.
The improved safety profile and higher reaction efficiency offered by flow chemistry resonate with both researchers and manufacturers. It enables the synthesis of complex molecules with higher yields and fewer unwanted by-products, contributing to cost savings and more sustainable practices. This driver aligns with the increasing emphasis on greener and more efficient chemical processes, making flow chemistry an attractive option for industries seeking innovative solutions that combine safety, efficiency, and reduced environmental impact.
Regulatory Compliance and Quality Control
The driver of regulatory compliance and quality control is a pivotal factor driving the adoption of flow chemistry in various industries. Flow chemistry offers a level of control and reproducibility that is highly valued in sectors such as pharmaceuticals, fine chemicals, and specialty materials. As regulations surrounding product quality, safety, and environmental impact become increasingly stringent, the ability to maintain consistent and well-characterized processes gains significance.
Flow chemistry’s precise control over reaction parameters, such as temperature, pressure, and residence time, enables manufacturers to ensure that reactions are conducted under optimized conditions. This translates to greater uniformity in product quality, minimizing batch-to-batch variations. The continuous nature of flow chemistry reduces the likelihood of human errors associated with manual batch processes, enhancing process robustness and reliability.
For industries subject to rigorous regulatory scrutiny, such as pharmaceuticals, adhering to current Good Manufacturing Practices (cGMP) is paramount. Flow chemistry’s real-time monitoring capabilities allow for immediate detection and correction of deviations from expected outcomes, supporting compliance with regulatory standards. This enhances both the safety of the manufacturing process and the quality of the final product.
Flow chemistry’s potential to streamline quality control processes also contributes to its attractiveness. The continuous nature of the flow approach allows for in-line monitoring and analysis, facilitating real-time adjustments to optimize reactions and ensuring that specifications are met consistently. This helps reduce waste and resource consumption while meeting regulatory requirements for process validation and quality assurance. These factors expand the growth of flow chemistry market.
Flow Chemistry Market Restraints
Initial Investment Costs
The restraint of initial investment costs stands as a significant hurdle in the adoption of flow chemistry technology within the market. While flow chemistry offers an array of advantages such as increased efficiency and improved safety, the setup and implementation of a flow chemistry system entail substantial upfront expenses. Establishing a functional flow chemistry system requires procuring specialized equipment, including microreactors, pumps, sensors, and automation tools, which can involve a substantial financial commitment. Moreover, the need for skilled personnel who can design, operate, and maintain these systems contributes to the overall investment.
For smaller companies, startups, or those with constrained budgets, the high initial costs associated with acquiring and integrating flow chemistry equipment can act as a deterrent. The economic feasibility of adopting flow chemistry must be carefully weighed against the potential benefits and long-term cost savings that the technology can offer. Larger organizations might also need to allocate resources for retraining staff or hiring experts in flow chemistry to effectively utilize the technology.
As the flow chemistry market evolves, advancements in technology and manufacturing practices might gradually help alleviate some of these initial investment constraints. However, in the current landscape, the need for substantial upfront capital to establish a functional flow chemistry system remains a restraint for many potential adopters. Addressing this challenge might involve seeking grants, funding opportunities, or partnerships to offset the initial costs and foster broader adoption of this innovative technology.
Complexity of Implementation
The restraint posed by the complexity of implementation presents a challenge to the broader adoption of flow chemistry technology in the market. While flow chemistry offers advantages such as precise control and enhanced reaction efficiency, transitioning from conventional batch processes to continuous flow setups can be intricate and demanding. The complexity lies in the need to reevaluate existing workflows, adapt protocols, and train personnel to operate and troubleshoot the new systems effectively.
Implementing flow chemistry involves not only the integration of specialized equipment such as microreactors, pumps, and sensors but also the design of suitable reaction pathways that capitalize on the technology’s benefits. This demands a deep understanding of chemical reactions, kinetics, and fluid dynamics. Companies might need to reconfigure laboratory spaces and invest time in training their teams to work within the flow chemistry framework.
For companies accustomed to well-established batch processes, the shift to a continuous flow approach can be met with resistance due to the perceived disruption and complexity. This is especially true when attempting to optimize intricate reactions, customize microreactors, or adapt to the unique requirements of different reactions.
Addressing the restraint of complexity of implementation requires strategic planning, education, and training initiatives. Collaborating with experts in flow chemistry, utilizing resources such as online courses and workshops, and fostering a culture of continuous learning within organizations can help alleviate this challenge. Additionally, manufacturers and technology providers can work together to develop user-friendly and intuitive systems that simplify the transition to flow chemistry, making it more accessible to a wider range of industries and professionals, acting as restraining factors for the flow chemistry market.
Flow Chemistry Market Opportunities
Pharmaceutical Industry
The pharmaceutical industry presents a compelling opportunity for the flow chemistry market. The intricacies of drug discovery and development require efficient and streamlined chemical processes, which align perfectly with the capabilities of flow chemistry. Flow chemistry’s ability to precisely control reaction parameters, such as temperature and residence time, is crucial for synthesizing complex molecules and active pharmaceutical ingredients (APIs) with high yields and purity.
One of the key advantages for the pharmaceutical sector is the rapid synthesis of compounds enabled by flow chemistry. This speed accelerates the drug development pipeline, allowing researchers to produce multiple compounds in shorter time frames for testing and evaluation. Additionally, the continuous nature of flow systems minimizes the risk of unwanted side reactions and increases reaction efficiency, crucial factors when dealing with expensive and sensitive starting materials.
Flow chemistry’s potential in process optimization is particularly valuable during the development of manufacturing routes for new drugs. The ability to quickly adjust parameters and explore reaction conditions enhances the efficiency of process development, leading to cost savings and reduced time-to-market. Furthermore, flow chemistry’s scalability is advantageous for transitioning successful lab-scale reactions to larger production volumes, ensuring consistency in quality and yields.
The pharmaceutical industry’s focus on precision, quality, and efficiency aligns with the strengths of flow chemistry. As regulatory bodies emphasize process understanding and control, flow chemistry’s ability to provide real-time monitoring and reproducibility is increasingly valuable. To seize this opportunity, collaborations between pharmaceutical companies and flow chemistry technology providers can lead to the development of customized systems and methodologies tailored to the specific needs of drug discovery and production. These factors provide new growth opportunities to the flow chemistry market.
Customization and Innovation
The opportunity of customization and innovation is a driving force within the flow chemistry market, allowing researchers and industries to explore new frontiers in chemical synthesis. Flow chemistry’s inherent flexibility offers a platform for tailoring reactions to specific requirements, leading to the creation of novel compounds and methodologies that might not be achievable through traditional batch processes.
Customization is particularly advantageous for complex reactions, where precise control over reaction conditions is paramount. Researchers can design microreactors and reaction pathways to accommodate unique reactivity profiles, enabling the synthesis of intricate molecules that were once deemed challenging. This customization extends to reaction optimization, enabling researchers to rapidly fine-tune parameters for maximum yield, selectivity, and efficiency.
The continuous nature of flow chemistry encourages innovation by encouraging the exploration of uncharted chemical territories. The ability to test various conditions in a controlled and systematic manner facilitates the discovery of new reaction pathways, catalytic processes, and synthetic strategies. This innovation can lead to the development of cutting-edge products, fine chemicals, and materials with diverse applications.
Moreover, flow chemistry’s potential for multi-step synthesis within a single system opens the door to more complex and efficient reaction sequences. Researchers can integrate various reactions seamlessly, reducing the need for intermediate isolation and purification steps. This innovation streamlines processes and conserves resources, contributing to cost-effective and sustainable production. These innovations offer new growth opportunities in flow chemistry market.
Flow Chemistry Market Challenges
Expertise and Training
The challenge of expertise and training stands as a significant hurdle in the broader adoption of flow chemistry within the market. Operating and maximizing the benefits of flow chemistry systems demands specialized knowledge that might not be readily available across industries or regions. The technology involves the interaction of various components such as microreactors, pumps, sensors, and automation systems, requiring a deep understanding of their functionalities, maintenance, and potential troubleshooting.
Effective operation of flow chemistry setups demands trained personnel who can design and set up the systems, as well as monitor reactions in real time. However, the shortage of experts proficient in flow chemistry techniques can hinder the technology’s widespread use. This is particularly true for smaller organizations or those lacking the resources to provide comprehensive training.
For researchers and chemists accustomed to traditional batch processing, the transition to flow chemistry requires a shift in mindset and skillset. The complex nature of the technology might deter some professionals from attempting to adopt it, especially if they lack access to training programs or educational resources.
Addressing the challenge of expertise and training requires collaborative efforts from academia, industry, and technology providers. Developing accessible training programs, workshops, and online resources can help bridge the knowledge gap. Collaborations between experienced flow chemistry experts and those new to the technology can foster knowledge transfer and skill development. Additionally, companies investing in flow chemistry systems might need to allocate resources for training their teams to ensure effective implementation and utilization of the technology.
By addressing the challenge of expertise and training, the flow chemistry market can create a workforce that is well-equipped to harness the technology’s capabilities, accelerating its adoption and fostering innovation across industries.
Transition from Batch Processes
The challenge of transitioning from traditional batch processes to flow chemistry presents a significant hurdle in the wider adoption of this innovative technology within the market. Flow chemistry introduces a paradigm shift, moving away from the familiar batch reactors where reactants are mixed in a single vessel. This transition necessitates a reevaluation of workflows, protocols, and mindsets, which can be met with resistance due to concerns about disrupting established practices and a lack of familiarity with the new approach.
Adapting to flow chemistry involves more than just implementing new equipment; it requires a fundamental shift in how chemists and researchers approach chemical reactions. Processes that worked well in batch systems might need to be reoptimized for continuous flow, considering factors like residence time, reagent compatibility, and the intricacies of microreactor design. This complexity can make the transition daunting, especially for organizations accustomed to well-established batch methodologies.
Moreover, the transition might require adjustments to research and development timelines, potentially leading to temporary disruptions in production. This can be a concern for industries with time-sensitive projects or tight schedules. The perceived risk of transitioning can deter companies from exploring flow chemistry’s potential benefits.
Addressing the challenge of transitioning from batch processes involves education, training, and gradual implementation. Offering comprehensive training programs that cover not only the technology but also strategies for smoothly integrating flow chemistry into existing processes can help alleviate concerns. Collaboration with experts in flow chemistry, either through partnerships or consultation, can provide invaluable guidance during the transition. By acknowledging and addressing the challenges associated with this shift, the flow chemistry market can help organizations successfully embrace the benefits of continuous flow processes.
Regional Trends
North America: The United States and Canada were among the leaders in flow chemistry adoption, particularly in the pharmaceutical and chemical industries. The region’s focus on innovation, research collaboration between academia and industry, and well-established infrastructure contributed to its prominence in the flow chemistry market.
Europe: Europe demonstrated significant interest in flow chemistry, driven by the region’s emphasis on sustainable practices and green chemistry. The European Union’s regulatory environment encouraged the adoption of cleaner and more efficient chemical processes, aligning well with the advantages offered by flow chemistry.
Asia-Pacific: The Asia-Pacific region showed growing interest in flow chemistry, particularly in countries like Japan and China. The region’s expanding pharmaceutical and chemical industries, coupled with a focus on technology adoption, contributed to the uptake of flow chemistry systems. China’s push for research and development in the field of chemistry also likely influenced the regional trends.
Key Players
Key players operating in the global Flow Chemistry market are Thermo Fisher Scientific, Inc., Corning Incorporated, Lonza, Biotage, Perkinelmer, Inc., Milestone Srl, Velocys PLC, CEM Corporation, Thalesnano, Inc., Parr Instrument Company, Syrris Ltd., Zaiput, Ehrfeld Mikrotechnik GmbH, Chemtrix, YMC America, AM Technology, PDC Machines, Uniqsis Ltd., H.E.L Group, Advion, Inc., Flowid BV, and Asynt Ltd.
PRICE
ASK FOR FREE SAMPLE REPORT