Global Machine Safety Market, By Component (Presence Detection Sensors, Programmable Safety Systems, Safety Controllers/Modules/Relays, Safety Interlock Switches, Emergency Stop Controls, Two-Hand Safety Controls), Industry (Process Industry, Discrete Industry), and Region – Industry Analysis and Forecast to 2030
The global Machine Safety market is expected to grow from USD 5.17 billion in 2023 to USD 7.75 billion by 2030 at a CAGR of 6.0%. The machine safety market is driven by an increasing emphasis on workplace safety and regulatory compliance. As industries deploy advanced machinery, the demand for robust safety solutions rises. Organizations prioritize safeguarding workers and assets, adhering to stringent safety standards. The need to minimize accidents and enhance operational efficiency propels the adoption of comprehensive machine safety systems.
Figure 1: Global Machine Safety Market Size, 2023-2030 (USD Billion)
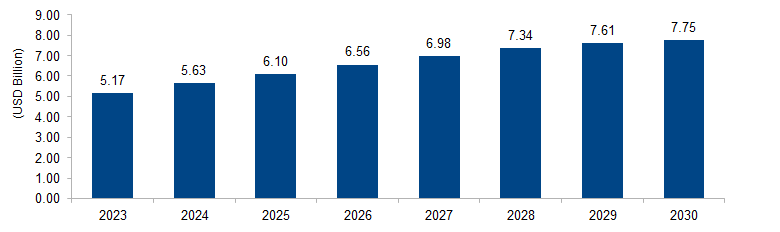
Source: Secondary Research, Expert Interviews, and MAARECO Analysis
Machine safety refers to the implementation of measures and systems to protect workers, equipment, and the surrounding environment from potential hazards associated with machinery and industrial processes. It involves the identification, assessment, and mitigation of risks, ensuring that machines operate safely and prevent accidents. Machine Safety encompasses the use of protective devices, safety procedures, and integrated technologies like sensors and interlocks to minimize the likelihood of injuries or damage. Compliance with international safety standards and regulations is crucial, emphasizing the integration of safety features during the design, installation, and operation of machines to create a secure working environment and prevent accidents in industrial settings.
Machine Safety Market Drivers
Stringent Regulatory Standards and Workplace Safety Requirements
A major driver of the Machine Safety market is the imposition of stringent regulatory standards and the increasing focus on workplace safety. Government bodies and industry associations worldwide are introducing and enforcing strict safety regulations to safeguard workers and prevent accidents. For instance, the Occupational Safety and Health Administration (OSHA) in the United States mandates compliance with safety standards such as ANSI B11 series. In the European Union, the Machinery Directive establishes essential health and safety requirements for machinery. As these regulations become more robust and comprehensive, industries are compelled to invest in advanced machine safety solutions to ensure compliance. The machine safety market responds to this driver by offering innovative safety technologies, including presence-sensing devices, safety interlocks, and safety-rated control systems, to meet evolving regulatory demands and enhance workplace safety.
Growing Automation in Industrial Processes
The increasing adoption of automation in industrial processes serves as a significant driver for the Machine Safety market. Industries are progressively integrating automated machinery and robotics to improve efficiency, productivity, and operational precision. As automation becomes prevalent, the need for advanced safety measures rises to mitigate the associated risks. According to the International Federation of Robotics (IFR), global sales of industrial robots reached approximately 373,000 units in 2020. The demand for safety solutions compatible with automated systems is on the rise to ensure that humans can work collaboratively with machines without compromising safety. Machine safety technologies, including safety-rated sensors and programmable safety controllers, are witnessing increased deployment to create a secure working environment amid the growing prevalence of automation across diverse industries, including manufacturing, logistics, and automotive production. The machine safety market aligns with this trend by providing solutions that facilitate the safe integration of automated processes in industrial settings.
Machine Safety Market Restraints
Cost Implications and Budget Constraints
A significant restraint in the Machine Safety market is the cost implications associated with implementing comprehensive safety solutions, leading to budget constraints for businesses. While the importance of ensuring workplace safety is acknowledged, the initial investment required for integrating advanced safety technologies can be substantial. According to the National Institute for Occupational Safety and Health (NIOSH), the costs associated with occupational injuries in the United States amount to billions of dollars annually. For businesses, especially small and medium enterprises (SMEs), the financial burden of adopting sophisticated safety systems may pose challenges. The need to retrofit existing machinery with safety features or invest in new safety-rated equipment can strain budgets, hindering widespread adoption. Striking a balance between safety and affordability remains a challenge, requiring the machine safety market to develop cost-effective solutions without compromising the effectiveness of safety measures.
Complexity in Integration and Retrofitting Challenges
The complexity in integrating machine safety solutions, particularly in existing industrial setups, poses a significant restraint. Many industries operate with legacy machinery that lacks built-in safety features. Retrofitting such machines with modern safety technologies can be intricate and time-consuming. The International Labour Organization (ILO) emphasizes the challenge of adapting safety measures to various types of machinery across industries. Integrating safety-rated sensors, programmable safety controllers, and interlock systems without disrupting production processes requires careful planning and skilled engineering. The retrofitting process may entail production downtime, affecting overall operational efficiency. Additionally, the diversity in machinery across industries introduces compatibility challenges when implementing standardized safety solutions. Overcoming these complexities requires collaboration between machine safety providers, industry stakeholders, and regulatory bodies to establish guidelines and best practices for seamless integration and retrofitting, addressing the diverse needs of different industrial environments.
Machine Safety Market Opportunities
Integration of Artificial Intelligence (AI) in Machine Safety
An emerging opportunity in the Machine Safety market is the integration of Artificial Intelligence (AI) technologies to enhance safety measures. AI can play a crucial role in real-time risk assessment and predictive maintenance, contributing to proactive hazard mitigation. The Industrial Internet Consortium (IIC) notes that AI applications in safety can lead to more than a 50% reduction in workplace accidents. Machine learning algorithms can analyze historical data to identify patterns, potential risks, and areas for safety improvement. AI-powered predictive maintenance can help prevent equipment failures, reducing downtime and enhancing overall safety. The opportunity lies in developing AI-driven machine safety solutions that adapt to changing work environments, continuously learn from data, and provide actionable insights to improve safety performance. As industries increasingly explore the potential of AI, the machine safety market can capitalize on this opportunity to offer innovative solutions that go beyond traditional safety measures.
Adoption of Collaborative Robots (Cobots) and Human-Robot Collaboration
Another significant opportunity for the Machine Safety market is the increasing adoption of collaborative robots (cobots) and the promotion of human-robot collaboration in industrial settings. The International Federation of Robotics (IFR) projects a substantial increase in the sales of collaborative robots, reaching an estimated 434,000 units by 2025. The opportunity arises in designing and implementing safety solutions tailored for human-robot collaborative environments. This involves developing advanced sensing technologies that enable robots to detect and respond to the presence of human workers, ensuring safe interaction. The market can explore innovations in safety-rated sensors, vision systems, and force-limiting technologies that facilitate close collaboration between humans and robots. With industries embracing automation, the demand for machine safety solutions compatible with collaborative work environments presents a fertile ground for the development of specialized safety technologies that foster efficient and safe human-robot interaction.
Machine Safety Market Challenges
Lack of Standardization and Harmonization
A significant challenge in the Machine Safety market is the lack of global standardization and harmonization in safety regulations. Diverse regions and industries often have their own set of safety standards and compliance requirements, leading to a fragmented landscape. The International Electrotechnical Commission (IEC) has made efforts to establish international standards such as IEC 62061 and ISO 13849, but widespread adoption remains a challenge. The absence of uniform safety standards complicates product development, testing, and compliance efforts for manufacturers and suppliers operating in multiple markets. This lack of standardization can result in increased costs and complexities for businesses seeking to provide machine safety solutions globally. Overcoming this challenge requires greater collaboration between international organizations, regulatory bodies, and industry stakeholders to establish common safety standards and promote harmonization, facilitating smoother global trade and the adoption of consistent safety practices across industries.
Evolving Cybersecurity Concerns in Connected Systems
A notable challenge facing the Machine Safety market is the evolving landscape of cybersecurity concerns, particularly in the context of connected and IoT-enabled safety systems. As machine safety solutions increasingly integrate with industrial networks and digital platforms, they become potential targets for cyber threats. The International Society of Automation (ISA) highlights the need for robust cybersecurity measures to protect safety-critical systems from unauthorized access, data breaches, and malicious attacks. The challenge lies in ensuring the resilience of interconnected safety systems against cyber threats while maintaining their functional integrity. The complexity of safeguarding connected machines and safety devices requires continuous advancements in cybersecurity technologies. Additionally, the machine safety market faces the challenge of raising awareness among end-users about the importance of implementing cybersecurity measures in conjunction with safety solutions. Collaborative efforts between cybersecurity experts, safety professionals, and regulatory bodies are crucial to addressing these challenges and establishing guidelines for secure integration of machine safety systems in the era of Industry 4.0.
Regional Trends
North America: In North America, the Machine Safety market has been influenced by a strong emphasis on workplace safety and compliance with regulatory standards. The Occupational Safety and Health Administration (OSHA) in the United States plays a crucial role in setting safety guidelines, driving the adoption of advanced safety technologies. The region has seen a trend towards the integration of Industry 4.0 technologies, including the Internet of Things (IoT) and artificial intelligence, to enhance machine safety measures. Collaborative efforts between industry stakeholders and regulatory bodies aim to address evolving safety challenges, with a focus on harmonizing standards and promoting the adoption of innovative safety solutions.
Europe: Europe has been at the forefront of promoting stringent safety standards and regulations. The Machinery Directive and other European standards guide safety practices in the region. Machine Safety trends in Europe include the increasing use of safety-rated components, such as sensors and controllers, and advancements in safety communication protocols. The European Agency for Safety and Health at Work (EU-OSHA) contributes to the development of safety initiatives. The region is witnessing a rise in the integration of safety systems with industrial networks, fostering smart and interconnected safety solutions.
Asia Pacific: The Asia Pacific region, driven by industrialization and increasing automation, has experienced a growing awareness of machine safety. Countries like China, Japan, and South Korea are witnessing a rise in the adoption of safety technologies in manufacturing and industrial processes. The Asia-Pacific Economic Cooperation (APEC) and national safety agencies contribute to safety standards. The market trends include a focus on developing cost-effective safety solutions to cater to a diverse range of industries in the region. Collaborations between international safety organizations and local stakeholders contribute to knowledge sharing and the implementation of best practices.
Middle East and Africa: In the Middle East and Africa, where industries like oil and gas, mining, and construction are prominent, there is a heightened focus on machine safety. The region experiences trends related to the integration of safety technologies in critical sectors, such as oil refineries and construction sites. The challenge lies in adapting safety measures to diverse industrial landscapes. Initiatives by regional safety authorities and industry collaborations contribute to shaping safety practices.
Latin America: Latin America sees a growing interest in machine safety, driven by developments in industries like manufacturing and agriculture. The region is experiencing trends related to the adoption of safety-rated components and the implementation of safety measures in diverse industrial applications. Latin American safety agencies and industry associations contribute to the development of safety guidelines, fostering a culture of safety in the workplace. The market trends include efforts to align with international safety standards and leverage advancements in technology for effective machine safety solutions.
Key Players
Key players operating in the global Machine Safety market are Schneider Electric, Honeywell International Inc., Rockwell Automation, Inc., ABB, Siemens AG, Omron Corporation, KEYENCE CORPORATION, Emerson Electric Co., Yokogawa Electric Corporation, Mitsubishi Electric Corporation, General Electric, Sick AG, HIMA, IDEC Corporation, Banner Engineering, Baumer, Pilz, Balluff GmbH, and Pepperl+Fuchs.
PRICE
ASK FOR FREE SAMPLE REPORT